Acktar, a world leader in light absorption, provides solutions for the suppression of stray light in wave lengths VIS, SWIR and MWIR.
With our super black materials, Foils and direct Coatings, we offer the blackening of opto-mechanical components. It is also available for light trapping applications such as lens housing, light baffle, IR sensor, UV sensor, passive infrared detector, black body, light detector, UV absorber, etc.
Our Metal Velvet™ Black Foil is the world's blackest black available as industrial coating that has below 1% total (hemispherical) reflectance at wavelength range 10nm-10,000nm. Metal Velvet™ has ultra-diffusive black matte finish exceeding major optical black paints and layers.
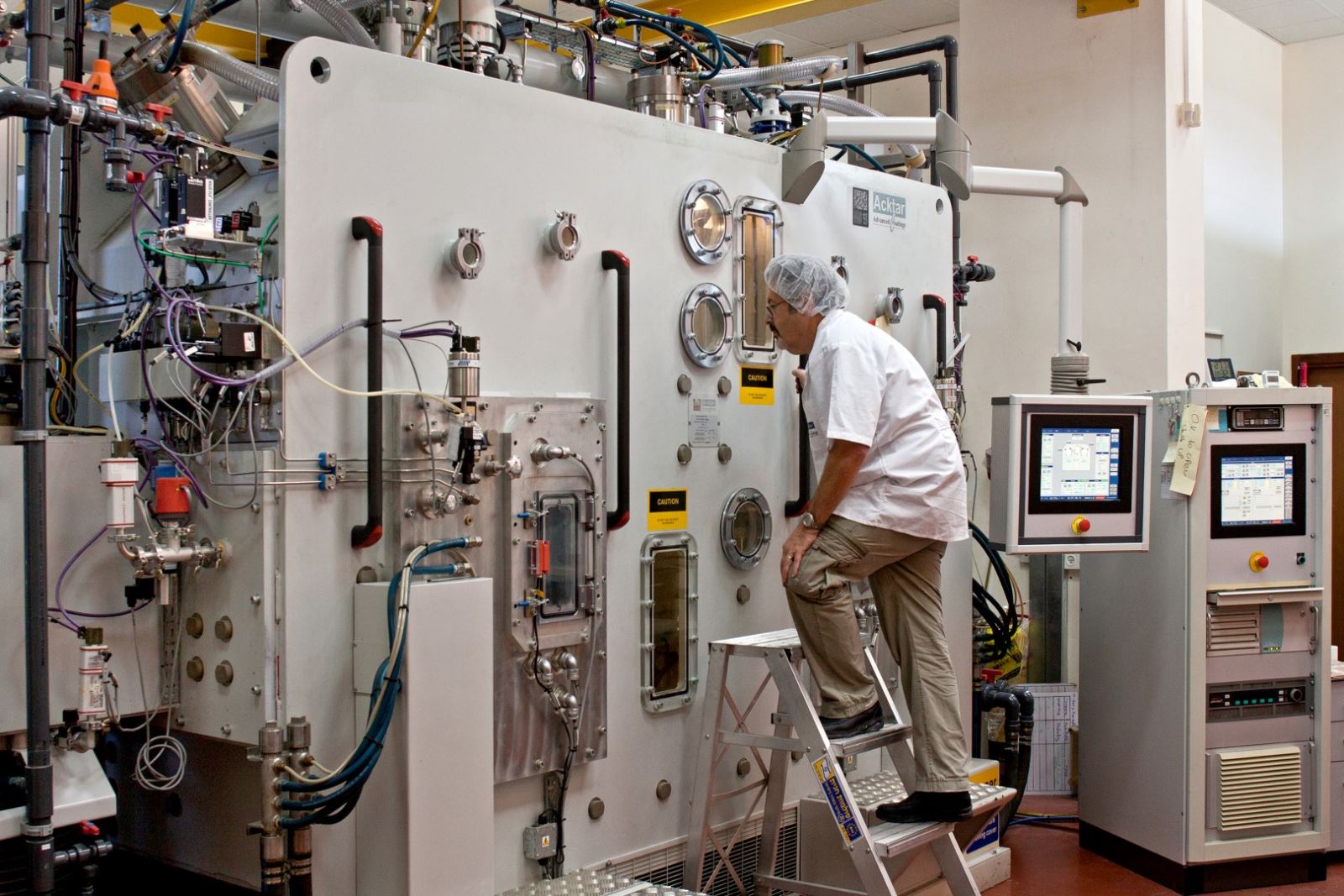
Applications of Acktar’s industrial coatings:
-
Internal parts of optical systems.
-
UV, Visible and IR light absorbing tapes.
-
High specific surface area coatings, replacing etching, graining, anodizing and other processes.
-
Cold shields and other IR detectors parts.
-
Emitters, blackbodies.
-
Thermal radiators for thermal control system (with pre-determined solar absorptance / thermal emittance ratios).
-
Parts for thermographic cameras, night vision systems.
-
Radiation absorbing layers for temperature sensors.
-
Heat dissipation coatings for electronic systems.
-
High capacitance anode and cathode foils.

Acktar’s Mission for the Environment
The environment is a key aspect in all Acktar’s activities. This includes our offices, process, product as well as a central part of all our R&D efforts.
Our Office: Acktar has recently gone paperless. To do so we added a new computerized system, allowing easy access to all necessary information. And any papers still found around are collected and recycled.
Our Process and Product: The basic nature of Acktar’s coating processes do not include the use of any environmentally damaging materials and therefore do not generate any undesirable waste. The process itself is an engineered surface with a controlled topology, created by vacuum deposition of inorganic and completely non-toxic materials on a substrate.
By replacing “old” processes such as: Chemical etching and anodizing, that include the use of environmentally dangerous materials and generate toxic waste, we eliminate all costs of treating toxic waste and can offer not only more competitive prices but provide a unique and higher quality of product, the basis for an ecologically friendly product.